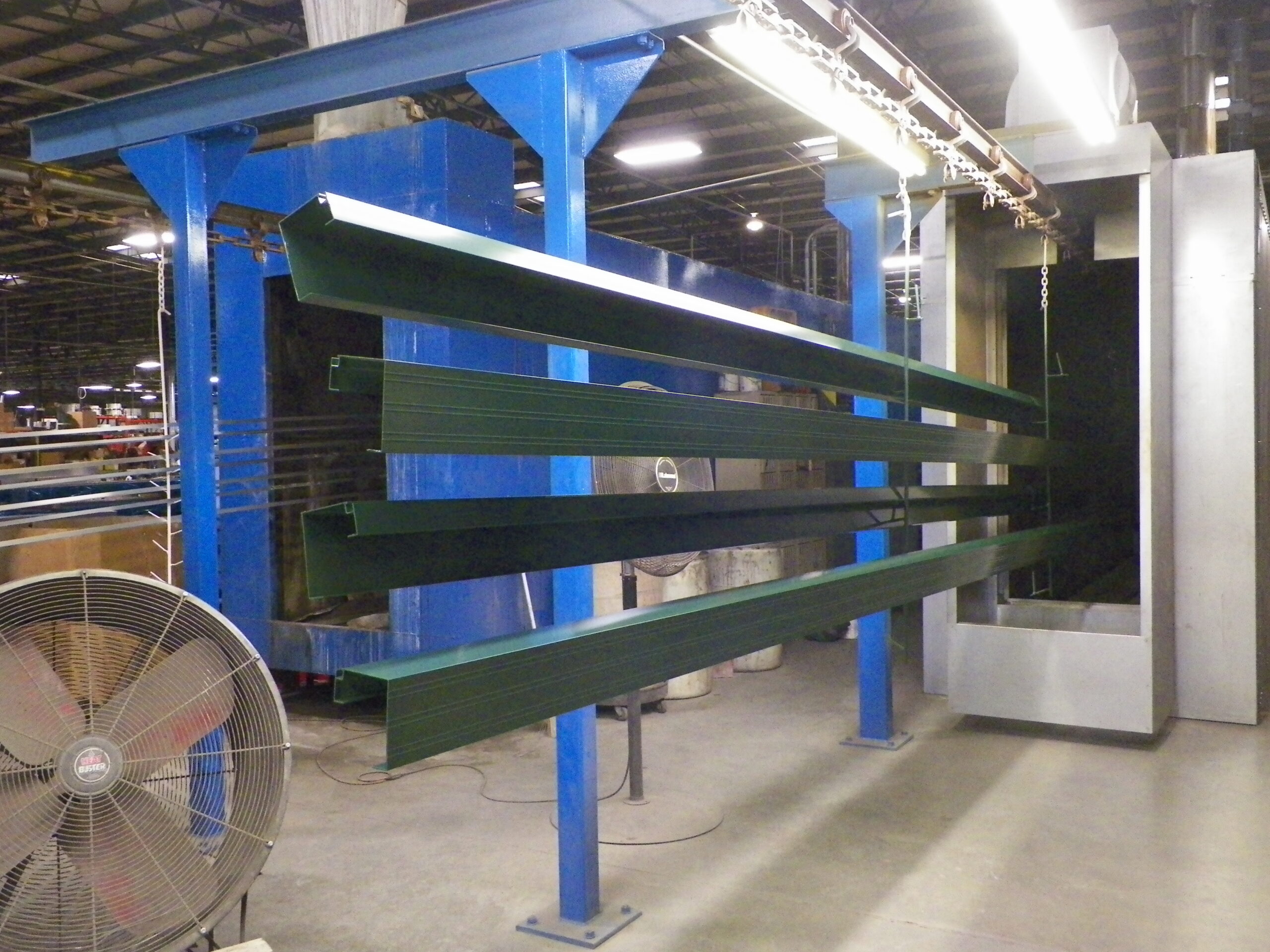
What Is Powder Coating?
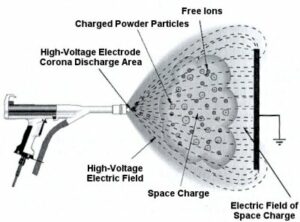
Powder coating is an advanced method of applying a decorative and protective finish to a wide range of materials and products that are used by both industries and consumers. The powder used for the process is a mixture of finely ground particles of pigment and resin, which is sprayed onto a surface to be coated. The charged powder particles adhere to the electrically grounded surfaces until heated and fused into a smooth coating in a curing oven. The result is a uniform, durable, high-quality, and attractive finish. Powder coating is the fastest-growing finishing technology in North America, representing over 10% of all industrial finishing applications.Powder coating is a type of coating that is applied as a free-flowing, dry powder. The main difference between a conventional liquid paint and a powder coating is that the powder coating does not require a solvent to keep the binder and filler parts in a liquid suspension form. The coating is typically applied electrostatically and is then cured under heat to allow it to flow and form a “skin”. The powder may be a thermoplastic or a thermoset polymer. It is usually used to create a hard finish that is tougher than conventional paint. Powder coating is mainly used for coating of metals
It Looks Like Paint But It Acts Like Armor
It’s tough. It looks great. And it lasts a long, long time. Powder coating is a superior finish that’s found on hundreds of products you come in contact with each day. It makes products durable, attractive, and scratch-resistant, too.
There are several advantages of powder coating over conventional liquid coatings:
- Powder coatings emit zero or near zero volatile organic compounds (VOC).
- Powder coatings can produce much thicker coatings than conventional liquid coatings without running or sagging.
- Powder coating overspray can be recycled and thus it is possible to achieve nearly 100% use of the coating.
- Powder coating production lines produce less hazardous waste than conventional liquid coatings.
- Capital equipment and operating costs for a powder line are generally less than for conventional liquid lines.
- Powder coated items generally have fewer appearance differences between horizontally coated surfaces and vertically coated surfaces than liquid coated items.
- A wide range of specialty effects is easily accomplished which would be impossible to achieve with other coating processes.
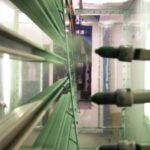
In 2010, the global demand for powder coatings amounts to approximately US$5.8 billion. Driven by the development of new material, new formulations and advancement of equipment and application processes, the powder coating market presents a rapid annual growth of around 6% from 2012 to 2018. Currently, the industrial uses are the largest application market of powder coatings. Automotive industry experiences the most dynamic growth. Steady and strong growth is also expected by furniture and appliance markets. Furthermore, the application of powder coatings in IT & Telecommunication is also being widely explored.
Pretreatment
Our 3 stage pretreatment system is designed to clean both steel and aluminum surfaces.
- Stage 1 has the dual cleaner heated to 140°F and sprayed at 15-25 psi. This stage removes soils.
- Stage 2 is a continuous overflowing, freshwater rinse and removes any excess cleaners.
- Stage 3 is the final seal rinse. Sealers are used to increase rust resistance without using environmentally harmful materials such as hexavalent chrome sealers.